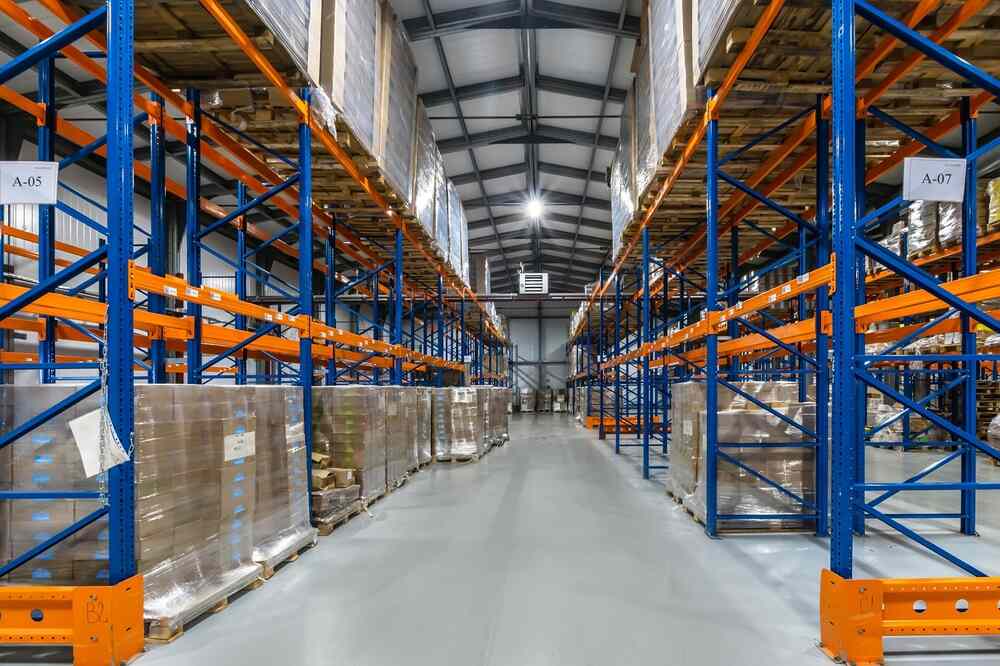
Running a warehouse that runs smoothly while meeting regulatory and operational standards is no small feat. Achieving warehouse operations compliance isn’t just about ticking off checklists—it’s about building a system that enhances efficiency, order accuracy, and overall performance. Whether you’re looking to optimize space, improve processes, or enhance the work environment, these six strategies will set you on the path to success.
1. Implement Warehouse Standard Operating Procedures (SOPs)
Warehouse standard operating procedures (SOPs) are the backbone of compliant and efficient warehouse operations. Clear guidelines ensure that warehouse staff understands their roles, processes, and safety protocols. Well-documented SOPs help minimize errors, streamline order processing, and keep operations consistent.
How SOPs improve compliance:
- They establish consistent practices for picking, packing, and shipping.
- They outline safety measures, reducing workplace accidents and liabilities.
- They ensure proper handling of sensitive inventory, supporting inventory control.
Regularly review and update your SOPs to address new challenges and opportunities in operations management.
2. Leverage Warehouse Management Systems (WMS)
Technology plays a vital role in modern warehousing operations. A warehouse management system (WMS) simplifies complex tasks like tracking inventory, managing orders, and monitoring performance. By integrating a WMS into your operations, you can optimize space in your storage areas, improve order accuracy and pick items faster, and track key performance indicators (KPIs) for continuous improvement.
For businesses wondering how to manage warehouse operations more efficiently, adopting a WMS is a no-brainer. It not only enhances compliance but also boosts productivity and customer service.
3. Prioritize Employee Training and Safety
A compliant warehouse isn’t just about technology—it’s about the people who make it all work. Training your warehouse workers ensures they understand proper procedures, safety guidelines, and operational goals. A safe and knowledgeable team reduces errors, enhances morale, and ensures a work environment that fosters productivity.
Key elements of effective training programs include educating staff on picking, packing, and shipping technique; teaching them how to handle hazardous materials safely; and providing ongoing education about updates to warehouse standard operating procedures.
By investing in your team, you’re also investing in improving warehouse operations.
4. Optimize Inventory Control and Space Management
Efficient inventory control is critical for compliance and operational success. Maintaining accurate inventory levels and organized storage areas minimizes errors and improves order processing times.
Tips for optimizing inventory control:
- Use barcoding or RFID technology to track inventory in real-time.
- Adopt a “first-in, first-out” (FIFO) method to reduce waste.
- Conduct regular inventory audits to ensure accuracy.
Meanwhile, optimizing your warehouse layout enhances efficiency. Designate zones for fast-moving items, seasonal products, and bulk storage to reduce picking times and streamline operations.
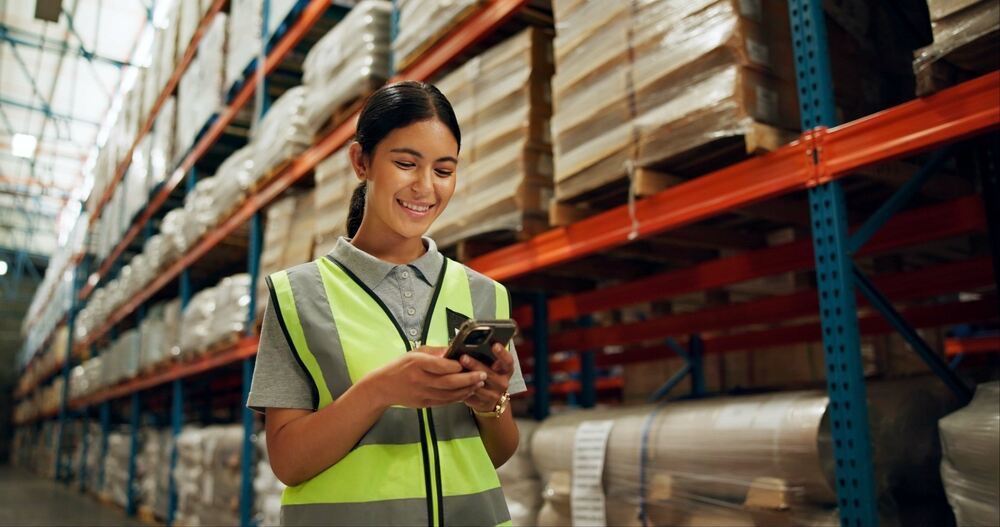
5. Monitor Key Performance Indicators (KPIs)
Tracking key performance indicators (KPIs) gives you insight into how well your warehouse is meeting compliance and performance goals. KPIs provide measurable data on critical aspects of warehouse management, helping you identify areas for improvement.
Essential KPIs to track:
- Order Accuracy Rate: Ensures customers receive the correct items, reducing returns.
- Order Cycle Time: Measures the time it takes to process and ship orders.
- Inventory Turnover: Tracks how quickly stock moves through the warehouse.
- Picking Efficiency: Evaluates the time it takes warehouse workers to locate and pick items.
By focusing on these metrics, you can pinpoint inefficiencies and implement strategies to address them, ensuring your warehouse runs smoothly.
6. Foster a Culture of Continuous Improvement
Compliance isn’t a one-time achievement—it’s an ongoing effort. To stay ahead, foster a culture of continuous improvement in your warehouse operation. Encourage your team to identify pain points and suggest ways to improve processes.
How to promote continuous improvement:
- Hold regular team meetings to discuss challenges and successes.
- Use data from your WMS to identify trends and areas for growth.
- Reward employees who contribute innovative ideas to improve operations.
When everyone is invested in improving the warehouse, you’ll find it easier to meet compliance standards and enhance overall performance.
The Bottom Line
Achieving compliance in warehouse operations involves more than just following rules—it’s about creating a system that maximizes efficiency, minimizes risk, and enhances customer service. By implementing these six strategies, from using warehouse management systems to prioritizing employee training, you’ll be well on your way to improving warehouse operations and maintaining a compliant, efficient environment.
Take the time to evaluate your current processes and identify opportunities to optimize space, streamline workflows, and ensure safety. With a focus on continuous improvement and modern technology, your warehouse will not only meet compliance standards but also thrive in a competitive market.