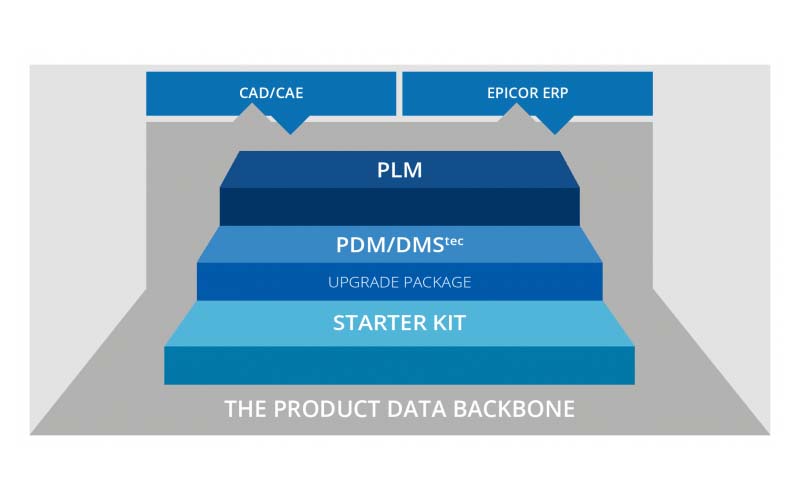
PDM System
Product Data Management (PDM system) represents the second step after CAD data management. While the latter is limited to the mere storage and retrieval of CAD data, Product Data Management connects drawings, documents and Bills of Materials and integrates them with a ERP, workflow or document management system (DMStec system), making the Product Data Management system a complete repository of all the data required to describe a product – from CAD, ERP, and PLM. Its purpose is to record and manage the results delivered by product engineering and product management and to make them available along the product lifecycle.
A PDM solution automates the exchange of Bills of Materials between the CAD system and the ERP system, maintaining transaction integrity and eliminating the need to manually enter them into the ERP system. Design and purchase items are also automatically synchronized. A customizable set of rules governs the synchronization of data, which can be managed and monitored from a single pane of glass in the PDM system, thereby bridging the gap between the ERP, CAD and PDM environments. This gives companies a reliable product data foundation by breaking down the product data silos created by product engineering, project management, maintenance, development, and production and making the information available across department lines. This enables designers to go through the PDM system to access supplier and material master data stored in the ERP system directly from their CAD workstation at any time. The risk of error is significantly reduced and companies save money and resources by eliminating the need for redundant development work.