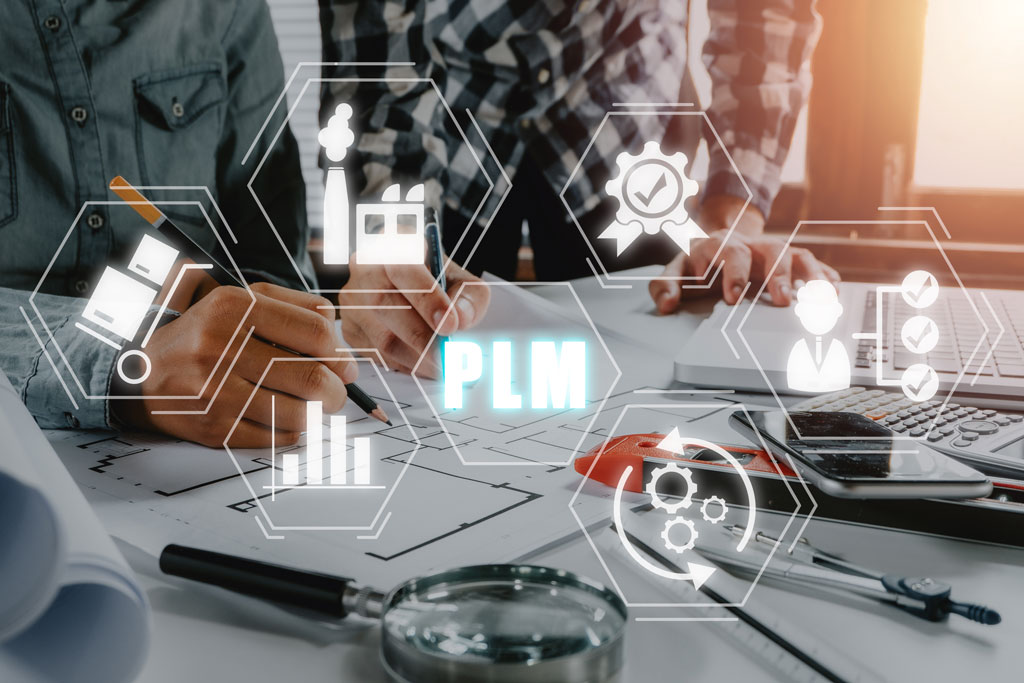
Effective Product Lifecycle Management (PLM) is essential for companies looking to streamline their product development process, improve quality, and reduce costs. However, achieving a successful PLM implementation requires careful planning and the adoption of industry-proven best practices. Whether you’re deploying a new PLM system or upgrading an existing one, these 11 best practices will help ensure a smooth transition and long-term success.
1. Define Clear PLM Objectives
The first step in any successful PLM deployment is to set clear goals. Why are you implementing PLM software, and what do you hope to achieve? Whether it’s improving product quality, reducing costs, or speeding up product launches, having clearly defined objectives will help you shape your implementation strategy.
Defining goals early on will also guide the project team and help keep everything on track during the deployment process.
2. Maintain High Data Quality
One of the most important aspects of PLM implementation best practices is ensuring that you maintain high data quality throughout the process. Clean and accurate data is crucial for making informed decisions, especially when managing the stages of the product lifecycle.
Before migrating data from an existing system, ensure that all records are complete and standardized. A well-organized database will save time, reduce errors, and prevent compliance issues as you transition to your new PLM solution.
3. Plan for Seamless Data Migration
Migrating data from your current system to a new PLM platform can be a complex process. PLM data migration best practices suggest starting with a detailed plan that maps out how data will move from your existing system to the new PLM environment. Verify data integrity before and after migration to ensure nothing is lost. This will allow for a smooth transition without causing any interruptions to business operations.
4. Engage Cross-Functional Teams Early
A successful PLM implementation involves more than just IT or project managers. Engaging cross-functional teams early on ensures that all stakeholders—whether in design and engineering, manufacturing, or quality management—contribute to the system setup. Their input is crucial for aligning the PLM lifecycle model with business processes, and it helps the system meet the specific needs of each department. Encouraging collaboration across departments from the beginning helps create a more efficient product management lifecycle.
5. Focus on Project Management Excellence
Effective project management is at the heart of any successful PLM implementation. You’ll need a project manager who can ensure tasks are on schedule, resources are allocated appropriately, and goals are met. Adopting PLM implementation best practices such as creating detailed timelines and risk mitigation strategies will help keep the project on track. Clear project management not only ensures a smooth rollout but also increases the likelihood of achieving the desired results.
6. Integrate with Existing Systems
For the best results, your PLM system should integrate seamlessly with your existing enterprise software, such as ERP or CRM systems. Integrating data between different platforms ensures consistency across the entire product lifecycle and improves decision-making processes. This integration eliminates redundant tasks and reduces errors, as your data sources are linked and synchronized. When you align your PLM with other key business systems, you unlock greater operational efficiency.
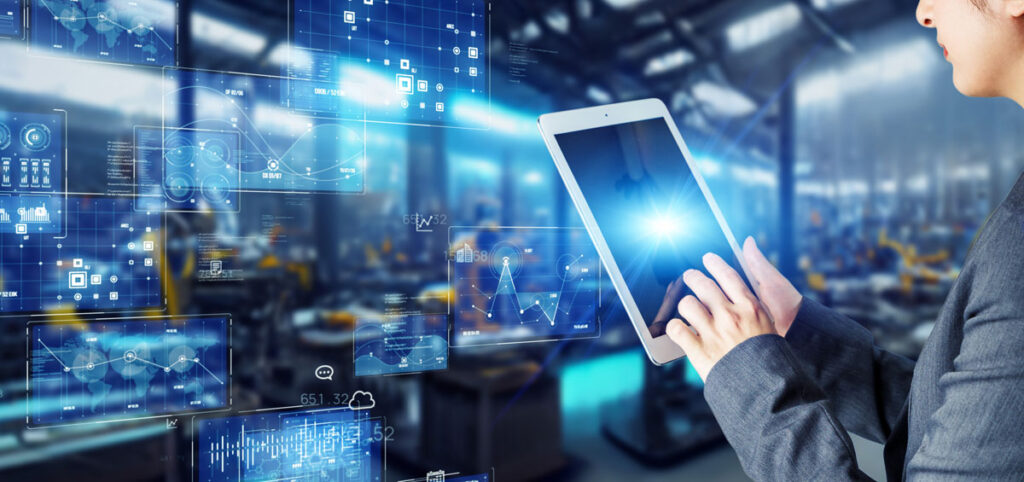
7. Prioritize User Training
A key PLM deployment best practice is prioritizing comprehensive user training. Training all relevant team members ensures that they understand how to use the new system effectively, which minimizes disruption and maximizes productivity.
It’s important to schedule ongoing training sessions to ensure that employees stay up-to-date with system updates and new features. Well-trained staff will also be better equipped to handle the system’s full capabilities, allowing them to make more informed decisions and contribute to continuous process improvements.
8. Leverage Analytics for Decision-Making
One of the major benefits of PLM is its ability to offer real-time insights into your product development process. With data analytics integrated into your PLM system, you can make data-driven decisions that improve efficiency and reduce time to market. Analytics help project managers and executives track the progress of products and understand key performance metrics, which in turn improves product quality and reduces costly errors.
9. Focus on Continuous Improvement
Successful PLM isn’t a one-time project—it’s an ongoing process. Regularly assess your PLM system and business processes for opportunities for continuous improvement. Use feedback from team members to adjust workflows, enhance system functionality, and streamline the management process. The goal is to create a system that grows with your organization and continues to add value over time.
10. Manage Costs Throughout the Lifecycle
Another important PLM best practice is to use the system to manage costs across the entire product lifecycle. From the design phase to final production, tracking expenses through your PLM system can help reduce overhead and prevent budget overruns.
For instance, with accurate tracking of material usage and labor, you can optimize the manufacturing process to minimize waste and ensure more efficient production. Cost management is a key factor in achieving long-term financial success with your PLM system.
11. Optimize for Faster Time to Market
The ultimate goal of PLM is to improve efficiency and reduce time to market. By following the best practices for product lifecycle management, such as integrating data sources and improving communication across departments, your organization will be better positioned to develop and launch products faster.
PLM software helps eliminate bottlenecks in the product development process, allowing your teams to work more efficiently and bring products to market ahead of the competition.
The Bottom Line: Achieving Long-Term PLM Success
By following these 11 essential PLM best practices, companies can successfully implement and manage their PLM systems to achieve long-term success. From ensuring data quality and integrating existing systems to optimizing for continuous improvement, these strategies provide a roadmap for creating an efficient and streamlined product lifecycle.
Whether you are managing a product portfolio, improving collaboration across teams, or aiming to deliver higher-quality products, adopting these PLM deployment best practices can give you the competitive edge you need. As you implement your PLM system, keep these best practices in mind to ensure a successful PLM implementation and position your business for growth in the future.