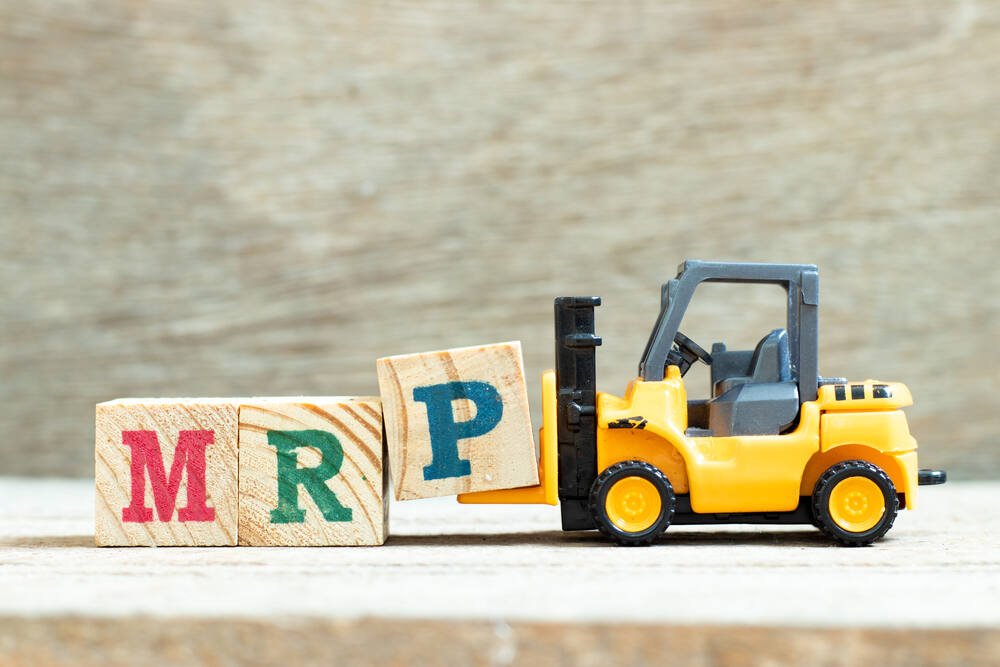
When it comes to streamlining operations, many manufacturing businesses turn to software solutions like ERP (Enterprise Resource Planning) and MRP (Material Requirements Planning). But what exactly are these systems, and how do they differ? If you’ve ever wondered about the difference between ERP and MRP, you’re not alone. Both are powerful tools for manufacturing operations and supply chain management, but they serve different purposes and address distinct business needs.
This guide explores ERP and MRP systems, highlighting how each function and when to use one over the other.
What is Material Requirements Planning (MRP)?
Material Requirements Planning (MRP) is a software-based approach to managing production and inventory in manufacturing processes. MRP focuses on ensuring that all materials and resources required for production are available when needed. By doing this, it helps businesses meet demand without overstocking or running out of materials.
The core functions of an MRP process include:
- Inventory Control: MRP ensures that raw materials are available for production, minimizing delays.
- Production Plan: With MRP, you can create a production schedule that optimizes manufacturing timelines.
- Managing Inventory: The software monitors inventory levels to maintain just the right amount of stock on hand.
- Bill of Materials (BOM): MRP systems track each material and component required, ensuring that nothing is missing when production begins.
In short, MRP is a tool specifically tailored for materials requirement planning and production needs in manufacturing businesses.
What is Enterprise Resource Planning (ERP)?
Enterprise Resource Planning (ERP) is a broader, all-encompassing system designed to manage an organization’s business processes across departments. While MRP is solely focused on materials and production, ERP software extends its functionality to finance, human resources, project management, sales, and beyond. By centralizing data from different departments, ERP software provides a single source of truth that helps companies operate more efficiently.
Key functions of an ERP system include:
- Supply Chain Management: ERP helps businesses coordinate their supply chain management activities, from purchasing materials to shipping finished goods.
- Inventory Control and Purchase Orders: ERP streamlines inventory management and purchase order processes.
- Capacity Planning: ERP assists with capacity planning to ensure production can meet demand.
- Financial Management: ERP software includes modules for managing accounting, payroll, and other financial functions.
By integrating these functions, ERP allows organizations to make informed decisions based on real-time data across their business processes.
The Difference Between ERP and MRP
So, what is the difference between MRP and ERP? While MRP is primarily focused on managing materials and production processes, ERP is a comprehensive system that connects all aspects of a business. Here’s a quick breakdown of how they compare:
- Scope: MRP focuses on production and materials, while ERP covers broader areas, including finance, HR, and supply chain.
- Functionality: MRP assists with materials requirement planning and inventory, while ERP helps manage entire business processes.
- Data Integration: ERP systems integrate data across departments, offering a holistic view. MRP, however, primarily deals with data related to production and inventory.
Think of MRP as a subset of ERP. Some ERP systems even include MRP capabilities, making it possible to address both production and enterprise-wide needs.
When to Use MRP
If your primary focus is managing materials, inventory, and production schedules, MRP software may be the best choice. MRP systems are ideal for manufacturers who need to streamline production planning without the added complexity of non-production functions.
MRP is beneficial for:
- Inventory Management: MRP keeps inventory levels in check, ensuring you don’t overstock or run short on materials.
- Production Planning and Scheduling: By focusing on the production plan, MRP helps meet manufacturing timelines efficiently.
- Managing the BOM: With a clear view of materials needed for production, MRP systems streamline bill of materials (BOM) management.
If you’re a manufacturing business that wants to optimize manufacturing processes and control materials without needing additional features like payroll or sales, an MRP system can be a cost-effective solution.
When to Use ERP
For companies looking to integrate multiple departments, ERP is the go-to solution. ERP allows businesses to centralize operations, break down silos, and gain a single source of truth across the entire organization.
ERP systems are suitable for:
- Comprehensive Business Management: ERP integrates processes across finance, HR, sales, and production.
- Capacity Planning and Inventory Control: ERP can plan production and manage inventory at a higher level, coordinating with other departments.
- Improving Decision-Making: ERP provides real-time data across the business, enabling better decision-making.
- Customer Relationship Management (CRM): ERP often includes CRM features, allowing companies to streamline sales and improve customer relationships.
ERP is ideal for larger organizations that need end-to-end visibility into their business processes and are looking for a more unified approach to managing products and operations.
ERP and MRP in Action: Key Use Cases
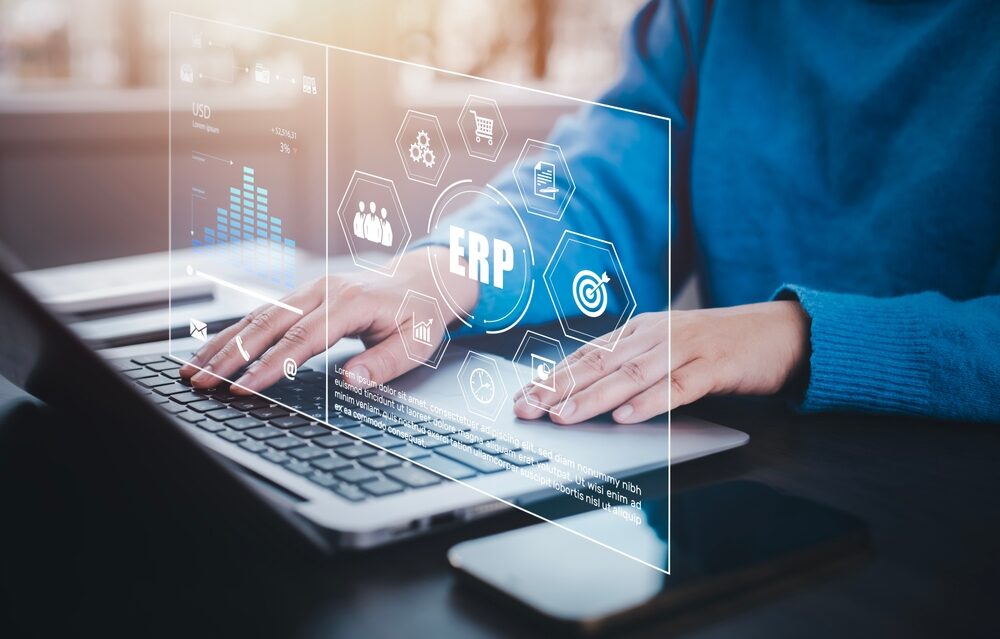
Both ERP and MRP serve important roles in manufacturing operations. Here’s how each system can support a typical production environment:
- ERP System Integration: A manufacturing business that relies on sales, finance, and production data may use ERP to connect these functions. ERP will support production processes while managing accounts, handling customer orders, and coordinating with suppliers.
- MRP Process for Production: A small manufacturer focused on production efficiency may implement MRP to optimize its production planning and inventory management. MRP helps ensure that materials are always available to meet production schedules without overstocking.
These examples demonstrate how ERP and MRP can work separately or together depending on the organization’s needs.
Benefits of ERP and MRP Systems
Here are some of the key benefits each system can provide:
Benefits of MRP
- Reduces Wasted Inventory: MRP ensures that materials are available without excess, reducing waste.
- Enhances Production Efficiency: By coordinating with the production schedule, MRP optimizes production flow.
- Improves Inventory Control: MRP provides a clear view of materials in stock and on order, helping with inventory control.
Benefits of ERP
- Centralizes Business Processes: ERP connects multiple departments, offering a single platform for the entire organization.
- Streamlines Supply Chain Management: ERP coordinates supply chain management activities, from procurement to finished goods.
- Supports Decision-Making: With real-time data, ERP systems help decision makers make informed choices across the business.
Choosing ERP or MRP for Your Business
Deciding between ERP or MRP comes down to your organization’s unique needs. For manufacturing businesses focused primarily on production and inventory control, MRP software may be sufficient. But for companies seeking a comprehensive approach to managing various business functions, an ERP system is the better choice.
In some cases, businesses may benefit from integrating both. Many ERP solutions offer built-in MRP functionalities, allowing you to manage materials and inventory within a larger system. This approach is particularly useful for larger organizations or those looking for growth, as it provides flexibility and scalability.
The Bottom Line
Understanding the ERP and MRP systems can help manufacturers improve manufacturing processes and align operations more effectively. While MRP focuses on the essential functions of materials requirement planning, ERP takes a broader approach, connecting multiple departments within an organization.
When choosing between ERP and MRP, consider your company’s size, growth goals, and specific needs. For businesses managing complex production and wanting to maintain a seamless flow from raw materials to finished goods, a combination of ERP and MRP may provide the most value.
Whether you choose ERP or MRP, both systems play a vital role in helping manufacturing businesses meet demands, stay competitive, and operate efficiently.